Do We Need Landing Pads?
As far as we can tell, we do need landing pads for missions that repeatedly visit a lunar outpost and for large, human-class missions to Mars. This is the consensus of the entire community of researchers that have worked on this problem — or at least, almost the entire community. We have not met any professional researchers in this field who believe we can do without them.
For lunar landings, our research has shown the sandblasting that will occur at a lunar outpost is unacceptable because it will excessively degrade optics, solar cells, thermal control surfaces, and moving joints on mechanisms. Impacts of blowing rocks could also break hardware.
For Mars landings, the deep cratering mechanisms fluidize a large volume of soil under the lander, and as the engine cuts off this soil is settling down and resolidifying at the same time the footpads are starting to bear the vehicle’s weight through that soil. The concern is that this process is unpredictable — we don’t normally land rockets on a fluid that freezes into solid at precisely the time we land on it. Even after landing, when the initial crater collapses, it may sap soil out from under the lander’s footpads causing the lander to tilt unpredictably. Also, rocks blown out of the initial crater will strike the bottom of the lander at high velocity and could damage the engine during critical portions of final descent. The astronauts will be six months away from any help we could send them. We need to solve the problem in a way that definitely controls these effects, and since we cannot definitely control fluidized soil under a large rocket, this means we need a solid surface instead.
The concept of landing pads can be interpreted broadly to mean any or all of the following:
- A concrete-like, impermeable surface that can handle high temperature and will not erode
- Gravel or polymer applied to the region surrounding this hard surface, to extend the region where soil does not erode
- Berms or fences surrounding the landing zone to block ejecta
- Blast barriers erected locally in front of critical hardware to protect them from the blast
Landing zones might also include
- Navigation beacons
- Lighting
- Roads to/from the outpost for repeated traffic
- Handling equipment to offload the landers
- Refueling systems for the landers
- Power systems to recharge batteries on rovers or landers
- Etc.
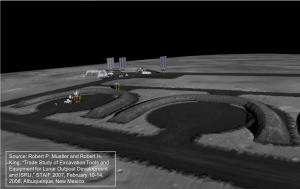
Evaluation of Landing Pad Technologies
Morris, Goldstein, et al. simulated a rocket exhaust interacting with a lunar berm or fence. Van Susante and Metzger performed calculations on the size of a landing pad needed to prevent soil eroding around its edges, and what size gravel can surround the landing pad to prevent erosion.
Van Susante, Metzger, Townsend, et al. performed tests of rocket thrusters firing on various lunar landing pad materials including compacted soil, tiles, and gravel. The experiments showed that gravel is not effective for the center of a landing pad because the gas travels through spaces between gravel and brings soil back up almost as if there gravel were not there. Tests with tiles showed that gas travels through the cracks between them and erodes the soil underneath, and the tiles can be flipped by gas building up underneath.
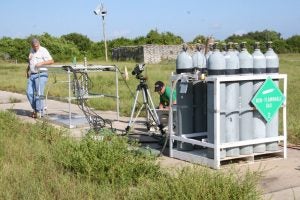
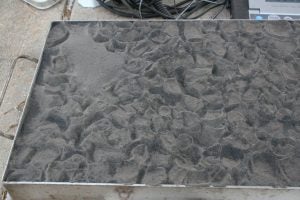
Mueller and team members of the KSC Swamp Works, along with the Pacific International Space Center for Exploration Systems (PISCES), and team members at Honeybee Robotics, partnered to test landing pad construction. A PISCES rover graded and compacted the soil. Swamp Works made interlocking tiles by sintering them from simulated lunar soil. The interlocking tabs on these tiles would prevent gas from flipping them over. A Honeybee robotic arm on a rover then assembled the tiles into a landing pad. This test demonstrated the feasibility of building landing pads on the Moon or Mars. More work is needed to perfect it because during a rocket firing the hot gas cracked a tile, built up high pressure under the pad, and caused catastrophic failure. Trenches for venting the gas from under the pad may solve this.
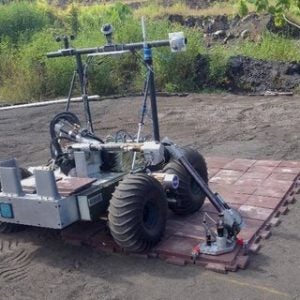
Paul Hintze has performed extensive research into methods of sintering, including resistive sintering and microwave sintering. He performed tests on a volcano with a robot sintering a patch of ground, and then it was tested by firing a small rocket thruster upon it.
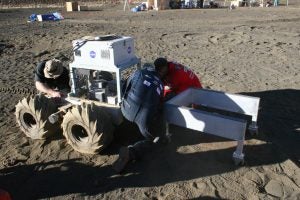
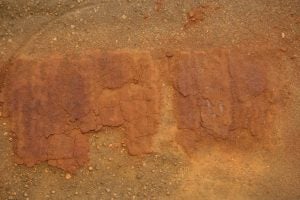